기사
BEV 기술이 발전하면서 판매량이 증가하고 있으나, 장기적인 생존 가능성을 결정 짓는 것은 차량의 안전성과 신뢰성이다
고도로 집적된 전력 모듈이 창의적인 가능성을 열어주며, 개별 솔루션보다 성능과 확장성이 훨씬 뛰어나다.
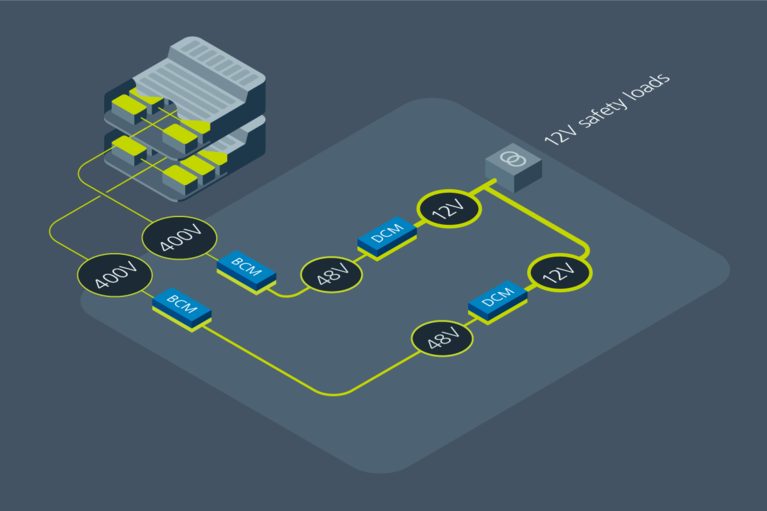
Patrick Kowalyk, 자동차 분야 FAE
전 세계적으로 전기차 판매가 계속해서 증가하고 있다. 2023년 3월에는 유럽 전역에서 BEV와 PHEV를 합쳐 322,000대 이상의 플러그인 전기차가 등록되었으며, 이는 전년 대비 29% 증가한 수치다. 그 중에서도 배터리 전기차(BEV)는 전년 대비 44% 증가했으며, 유럽 전체 자동차 판매의 16%를 차지했다[1]
이러한 수치는 2020-2021년 COVID-19 기간의 침체 이후 모든 자동차 제조업체에게 반가운 소식이라 할 수 있다. 전체 판매량의 반등과 전기차 판매의 급증은 미래의 긍정적인 신호다. 하지만 여전히 소비자들은 충전 인프라와 배터리 주행 가능 거리 문제에 대해 우려를 갖고 있다. 이에 대응해 제조업체들은 이미 소비자의 우려를 해결하기 위한 2세대 전기차 모델을 생산하고 있다.
2세대 전기차를 형성하는 트렌드들
몇 가지 주목할 만한 트렌드가 있다.
-
바로 충전 시간을 단축하고 차량 무게를 줄이려는 노력이다. 차량 무게는 전기차의 주행 거리에 직접적인 영향을 준다. 따라서 무게를 줄이면 적재 중량과 최대 주행 거리 모두를 향상시킬 수 있다.
-
기존의 12V 직류 DC를 제거한다면 상당한 무게 감소 효과를 누릴 수 있다. 오늘날에는 배터리 크기를 줄이거나 완전히 제거하는 것도 가능한 선택지다.
-
48V 존(zonal) 네트워크 아키텍처로 전환한다면, 부피가 크고 무거우며 비용이 많이 드는 전선 하니스의 필요성을 줄일 수 있다. 마찬가지로, 48V 아키텍처를 시트 히터나 시트 조정 장치 같은 보조 장비에 적용하면 케이블 크기와 무게를 줄이는 데 도움이 된다.
- 배터리 전압을 400V에서 800V로 업그레이드하는 트렌드 역시 빠르게 확산되고 있다. 이러한 변화로 케이블 무게와 충전 시간이 줄어들 수 있지만, 이를 뒷받침하기 위해선 충전소 인프라 역시 두 전압을 모두 지원할 수 있도록 업그레이드되어야 한다.
그럼에도 불구하고, 여전히 중요한 안전성과 신뢰성 개선이 필요하다. BEV는 모든 전력을 하나의 고전압 구동 배터리에서 얻기에, 이 전원이 끊긴다면 단순한 불편을 넘어 심각한 안전 문제로 이어질 수 있다. 따라서 현재 소비자들이 다양한 편의 기능에 끌려 전기차를 선택하고 있다고 하더라도, 장기적인 생존 가능성은 차량에 설계된 탄탄한 안전 프로토콜에 달려 있다. 완전 전기차에서 전력 이중화는 필수 요소이다.
전력 이중화 설계는 안전성과 신뢰성 확보에 필수적
전기차에 보조 전원을 추가할 시 운전자, 탑승자, 그리고 도로 위 다른 사람들에게 안전성과 신뢰성을 보장할 수 있다. 이중 전력은 다음 세 가지 부하 유형에 필요하다:
-
조향, 제동, 안전 센서 시스템
-
Always-on 차량 통신망(CAN 버스, 이더넷 등)
- 전력 위기 상황에서 꺼도 되는 비필수 부하들
예시로, 전기차 전력 설계자는 두 개의 400V 배터리 팩을 직렬로 연결하고, 별도의 DC-DC 변환기(400V에서 800V로 변환)가 연결되는 800V 구동 배터리를 구성할 수 있다. 이러한 구성(그림 1)은 '듀얼 400V 직렬 스택 시스템'이라 한다.
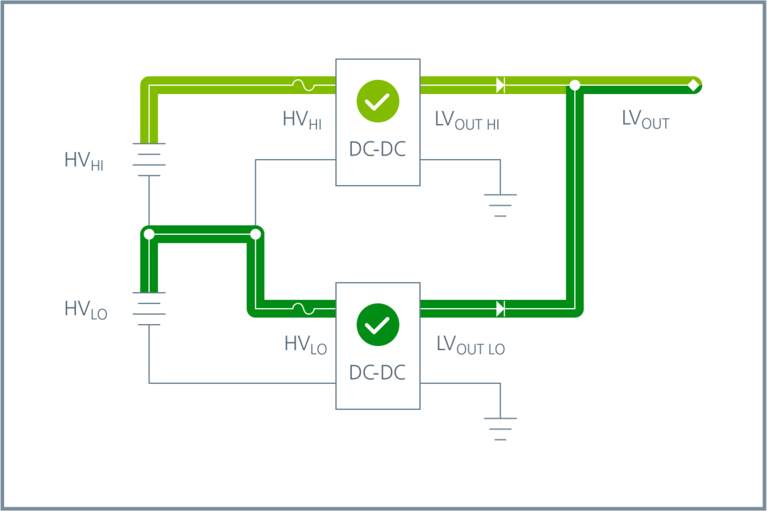
그림 1: 듀얼 400V 직렬 스택 시스템 두 개의 400V 배터리 팩을 직렬로 연결하고, 각 배터리에 개별 DC-DC 변환기를 사용하는 스택 아키텍처는 저전압 동작을 가능하게 하며, 부하를 두 개 이상의 회로로 분산시킬 수 있다.
현재 일부 제조업체들이 듀얼 400V 직렬 스택 시스템을 사용하는 데에는 몇 가지 이유가 있다. 가장 큰 이유는 현재 설치되어 있는 공공 충전기 중 상당수가 800V를 지원하지 않기에 400V 충전기로 충전하는 것이 더 용이하기 때문이다. 최근 설치되는 신형 충전기는 400V와 800V 배터리 모두를 지원할 수 있다. 또 다른 이유는, 만약 제조업체가 이미 400V 배터리 팩을 설계하고 인증까지 마친 상태라면, 이를 두 개 직렬로 추가하는 방식이 더 빠르고 쉽기 때문이다.
한편, 또 다른 방식으로는 듀얼 800V 병렬 배터리 구성이 있다(그림 2). 이 방식은 두 개의 800V 배터리를 병렬로 연결하는 것이며, 역시 개별 DC-DC 변환기를 두 개 사용해 전력 이중화가 가능하다.
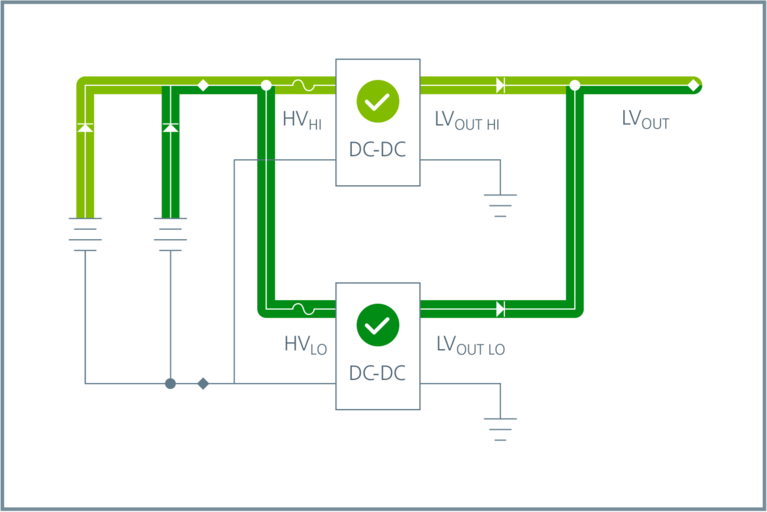
그림 2: 듀얼 800V 병렬 배터리 구성 이 구성은 저전류 운전을 가능하게 하며, N+1 이중화 구조를 구현하는 데 더 쉽다.
두 가지 구성 모두 장단점이 있다. 듀얼 400V 직렬 스택 시스템의 단점:
- 400V DC-DC 변환기는 최상단 변환기가 800V에 위치하게 되기에 차체 접지와의 간격이 더 필요하다.
- 두 개의 400V 배터리 팩 사이의 센터 탭(center tap)은 고전압 커넥터에서 접근 가능해야 한다.
- 두 배터리 팩 간의 전압 불균형이 발생하면, 조정기가 과전압 보호 모드에 들어가 전력 공급이 중단될 수 있다.
이 시스템의 장점:
- 한 회로(string)에 문제가 생기면 다른 회로가 부하를 담당할 수 있다.
- 시스템 구성 요소들의 전압 등급이 낮기 때문에 더 저렴하다.
- 두 개의 출력을 직렬로 연결하여 24V 출력을 만드는 것이 더 쉽다.
듀얼 800V 병렬 배터리 구성의 장단점.
장점:
- 400V 구성보다 운용이 더 안정적이다.
- 병렬 연결된 상태에서는 두 배터리 팩이 항상 동일한 전압을 유지하기 때문에 충전이 더 단순하다. 전체 800V 전압원이 병렬 구조 전체에 적용된다. 그렇기에 충전이 용이하다.
단점:
- 설계 관점에서 고전압 안전을 위해 차체와의 간격이 더 필요하다.
- 800V 전압 간에 단락이 발생할 시 시스템 전체가 종료된다.
현재 듀얼 800V 배터리 플랫폼을 사용하는 차량은 많지 않지만, 이 구성이 제공하는 이중화 기능은 안전 측면에서 매우 중요하다. 이중화가 없다면, 차량의 핵심 시스템은 단 한 번의 단락으로도 치명적인 결과에 이를 수 있다. 전기차의 전력 아키텍처는 이 방향으로 나아가고 있다. 신뢰성과 안전성이 이러한 전환의 가장 큰 이유이며, 최신 충전기들이 400V와 800V를 모두 지원함에 따라 시장에서도 점차 800V 쪽으로 방향이 기울고 있다.
어떤 구성을 선택할지는 다양한 요소에 따라 달라지겠지만, 대부분의 경우 듀얼 800V 배터리 구성이 선호된다. 그 이유는 단순하다. 이 시스템은 병렬 배터리를 사용함으로써 이중 전력 경로를 쉽게 구현할 수 있기 때문이다. 이로 인해 단락 발생 시에도 두 번째 전력 경로가 부하에 전력을 공급할 수 있어 시스템 전체의 종료를 방지할 수 있다.
물론 두 개의 배터리 팩을 수용하기 위한 공간과 중량, 주행거리 등 고려사항은 있다. 배터리 관리 시스템(BMS)을 위한 추가 회로가 필요하긴 하지만, 안전성과 신뢰성 측면에서 얻는 이점은 그보다 훨씬 크다.
전력 이중화의 다양한 형태 – 무엇이 최선인가?
이중화 구현에는 여러 가지 방법이 있으며(그림 3), 두 개 이상의 DC-DC 변환기를 통해 부하를 공유하고, 한 변환기가 고장 시 전체 부하를 담당할 수 있도록 설계할 수 있다. 전기차에 견고하고 신뢰성 높은 전력 아키텍처를 설계하는 것은 매우 도전적인 작업이다. 하지만 이중화를 도입하면 차량의 안전성과 신뢰성은 물론 소비자의 신뢰까지 향상시킬 수 있다.
이중화는 다양한 형태로 구현될 수 있다. 전원 공급 경로 전체를 출발점부터 부하 지점까지 살펴보고, 다음과 같은 질문을 던져야 한다,
- 이 지점 또는 회로 구간에서 고장이 발생하면 어떤 영향이 있는가?
- 차량은 계속 주행할 수 있는가?
- 어떤 기능이 작동하지 않게 되는가?
목표는 주행을 계속할 수 있거나 최소한 안전하게 고속도로 출구까지 이동할 수 있는 상태를 유지하는 것이다.
DC-DC 변환기에서의 이중화는 다양한 형태로 구현될 수 있다(그림 3). N+0, N+1, 2N+1 등의 예시가 있으며, 각 구성은 크기, 비용, 복잡성 측면에서 장단점이 있다. 따라서 차량별 아키텍처에 대해 면밀한 검토가 필요하다.
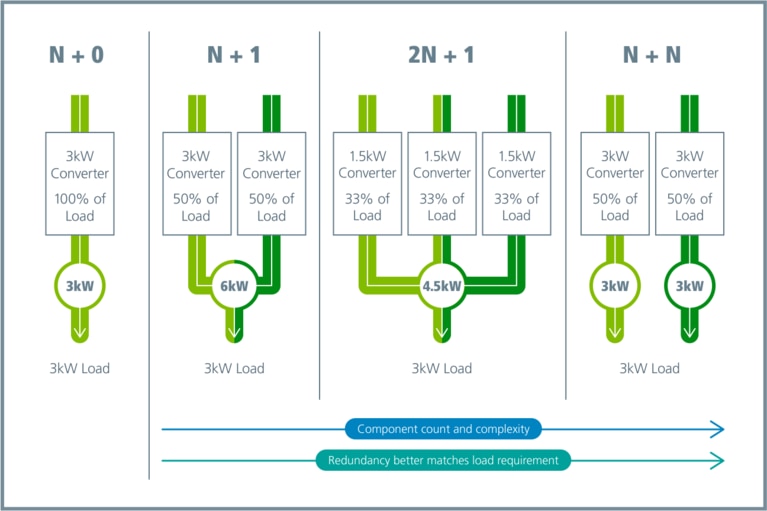
그림 3: 전기차 파워트레인에서 전력 수준과 전력 분배를 보여주는 다양한 이중화 구조 조합. N+1 구조는 더 큰 전력 처리 능력이 가능하므로, 크기가 커지고 비용도 높아질 수 있다. 왼쪽에서 오른쪽으로 갈수록 이중화 수준은 향상되며 전원 공급이 부하 요구에 더욱 밀접하게 맞춰지지만, 동시에 구성 요소 수와 시스템 복잡도도 증가한다.
양방향 DC-DC 변환기를 사용하고 차량 내 부하를 분리하면, 하나의 존에서 다른 존으로 전력을 전달할 수 있다. 조정기를 통해 전력을 전달하면 안정적인 전원 공급원이 되어 부하를 구동하거나 심지어 배터리를 충전할 수도 있다.
하지만 현재의 변환기 기술로는 DC-DC 변환기 유닛 여럿을 병렬로 사용할 수 있도록 작고 가볍게 만들기엔 기술적 제약이 있다.
Vicor의 BCM® 및 DCM™ 전력 모듈은 병렬 구성을 간편하게 구현할 수 있도록 지원한다. 이 모듈은 소형화되어 전체 DC-DC 변환기의 공간을 줄일 수 있으며, 효율성과 전력 밀도를 높여 성능을 향상시킨다(그림 4). 이는 차량의 주행 거리 향상뿐 아니라 안전성을 높이는 새로운 아키텍처가 가능해진다.
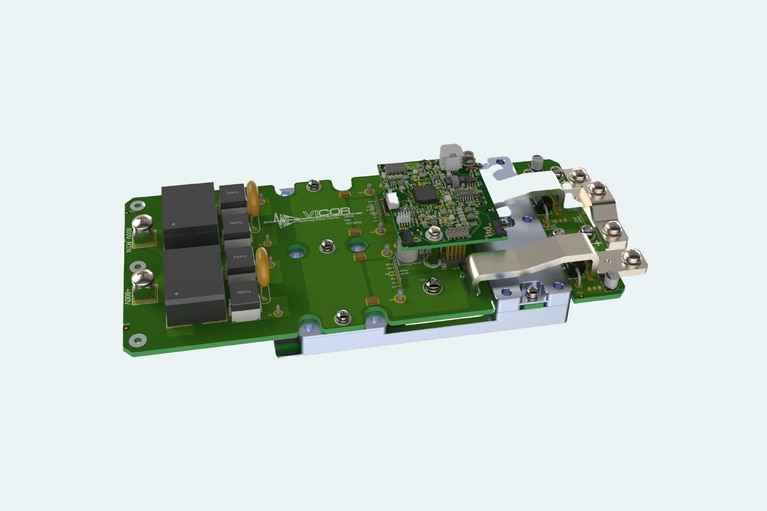
그림 4: 이 4kW DC-DC 변환기는 두 개의 Vicor BCM6135와 두 개의 DCM3735(기판 하단에 장착)를 사용하여 무게는 0.08kg, 부피는 단 0.8575L에 불과한 패키지에서 800V를 12V로 변환한다. 이 구성은 2kW씩의 이중 전원 공급으로 설정할 수 있으며, 다른 유닛과 병렬로 연결하여 이중화된 4kW 전원 공급장치로 구성할 수 있다.
고밀도 전력 모듈으로 설계상의 창의성이 가능해지고, 개별 디바이스 솔루션보다 성능과 확장성이 훨씬 우수하다. 전력 모듈은 최대 3배 더 높은 전력 밀도를 제공하며, 손쉽게 확장할 수 있고, 빠른 과도 응답 속도로 인해 12V/48V 보조 배터리를 소형화하거나 제거하는 것도 가능하게 한다. BCM(그림 5)은 고측(high-side) 전압을 낮춰주는 동시에 전류를 증폭시키고, 절연 기능도 제공하는 고밀도 고효율 변환기다.
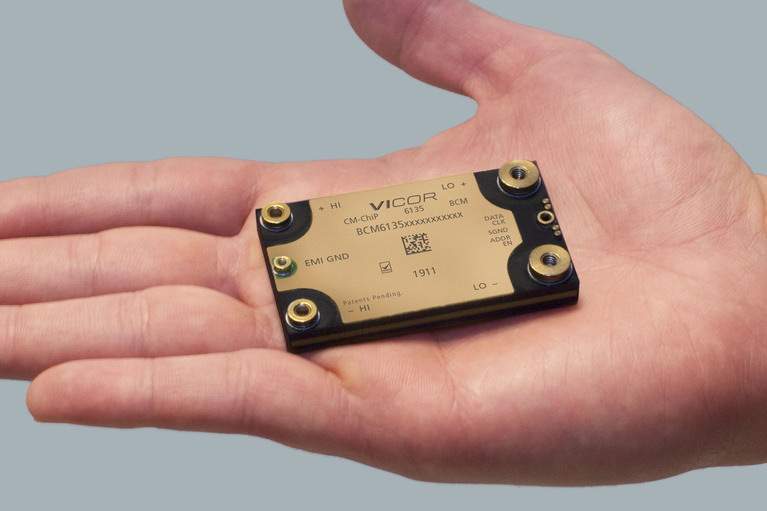
그림 5: BCM® 버스 컨버터 BCM은 고밀도, 고효율의 고정 비율(비조절형) 절연형 DC-DC 변환 모듈이다. 이 제품군은 800V 또는 400V 입력에서 48V로 변환되며, 다양한 K 계수를 적용하여 다양한 응용 환경에 맞게 구성할 수 있다. BCM은 고전압 배터리를 저전압 네트워크로 변환하는 데 가장 높은 전력 밀도를 제공한다. BCM 제품군은 Vicor의 Sine Amplitude Converter™ 기술을 기반으로 하며, 소형 모듈에서도 고효율을 구현할 수 있다. Vicor는 BCM을 400V 또는 800V 배터리와 맞추어 개발하고 있으며, 필요한 전력 수준에 따라 여러 개를 배열(array)로 구성할 수 있다.
BCM은 비율기(ratiometric) 장치로, 출력은 입력 전압에 K 계수를 곱한 비율로 나타난다. 예를 들어, 소스가 800V이고 병렬 구성이며 K 계수가 1/16이라면, 저측(low-side) 전압은 800V ÷ 16 = 50V이며, 출력 전류는 입력 전류 × 16이 된다. 듀얼 400V 직렬 스택 시스템 또한 유사한 BCM을 사용하는데, 이때는 K 계수가 1/8이다.
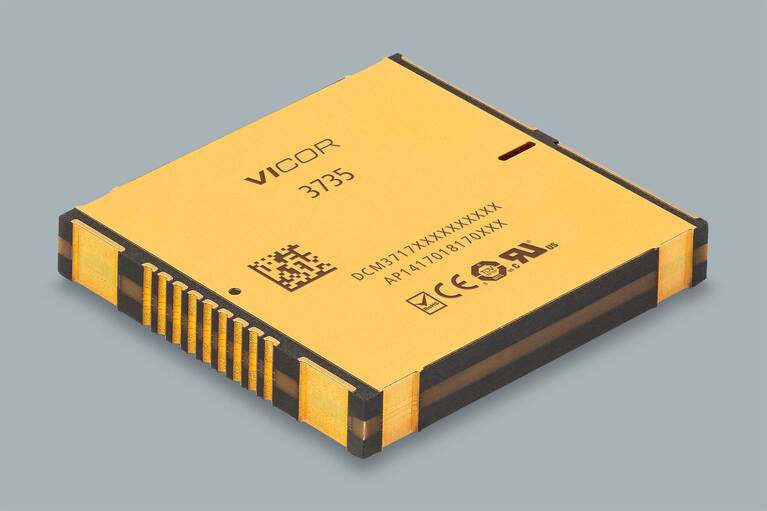
그림 6: DCM3735는 절연되지 않은 조절형 DC-DC 변환기로, 입력 전압 범위는 35-58V이다. 이 장치는 배터리 충전을 위한 정전류(상수 전류) 동작을 제공하며, 컴팩트한 크기(36.6 x 35.4 x 7.4mm)의 패키지로 제공되며 배열(array) 형태로 사용 가능하다.
DCM3735 조정기는 BCM으로부터 전압을 받아, 커패시터나 배터리를 충전할 수 있는 정밀하게 조정된 출력을 제공한다(그림 6). BCM과 DCM의 조합은 EV(전기차) 설계자들에게 공간과 무게를 효율적으로 절감하면서도 이중화된 전력 네트워크를 설계할 수 있는 유연성을 제공한다. Vicor의 기술은 0.9L 미만의 부피로 800V를 12V로 변환하는 4kW급 전원 공급을 가능하게 한다. 그림 4에서 볼 수 있듯이, 이 시스템의 무게는 1kg 미만이며, 12V 백업 배터리의 소형화를 통해 추가적인 무게 절감도 가능해진다.
소비자들은 전기차 구매를 원하지만, 여전히 망설이게 만드는 요인이 있다. 그중 가장 큰 우려는 주행 거리와 충전 편의성이다. 이 문제들은 해결이 간단하지 않지만, 전력 아키텍처 및 전력 밀도에 대한 새로운 혁신이 매우 큰 도움을 주고 있다. 컴팩트한 전력 설계 혁신은 차량 무게를 줄일 수 있고, 이는 곧 주행 거리 개선으로 이어진다. 또한 전력 모듈을 도입하면서 크기와 무게를 줄이는 데 있어 설계상의 창의성과 단순성이라는 장점이 발생하며, 결과적으로 더 긴 주행 거리를 가능하게 한다.
전력 모듈은 주행 거리, 신뢰성, 안전 문제를 해결하는 데 있어 핵심 요소다. 이 모듈은 작은 크기와 높은 확장성을 바탕으로 전력 시스템 설계에 큰 유연성을 부여한다. 혁신적인 아키텍처와 결합될 때, 전력 모듈은 오늘날 배터리 전기차의 장기적인 채택을 앞당기는 핵심적인 촉매 역할을 할 수 있다.
출처:
[1] Kane, Mark (2023년 5월 10일), “Europe: Plug-In Car Sales Accelerated In March 2023”, INSIDEEVS
Patrick Kowalyk은 6년 이상 자동차용 전력 시스템을 제공해왔으며, 수십 년간 현업에서 활동해온 엔지니어이다. Patrick의 깊이 있는 기술 지식은 Vicor의 자동차 사업 성장에 핵심적인 역할을 해왔으며, 전력 모듈, 회로 토폴로지, 아키텍처 전반에 걸친 전기공학적 전문성은 타의 추종을 불허한다. Patrick은 OEM과 티어1 고객사를 위한 컴팩트하고 효율적인 전력 시스템 설계를 도와온 중요한 인물이다. 일리노이 공과대학교(IIT)에서 전기공학 학사 학위를 취득한 바 있다.

패트릭 코왈릭(Patrick Kowalyk), 북미지역
자동차 애플리케이션 분야 수석 엔지니어
이 기사는 원래 출판사 Elektroniknet.de.