Article
BEVs have a weight problem that can’t be solved with traditional approaches
BEVs are getting heavier and adopting a 48V zonal architecture is needed to reduced weight and space. High-density power modules reduce weight, enhance efficiency and optimize the benefits of transition to 48 volt bus.

By Noa Margolin, R&D Engineer
High-density power modules enable 48V systems that reduce weight and power loss
Battery-electric vehicles (BEVs) have a serious weight problem and not the type Weight Watchers® can fix. Many BEVs are as much as 33% heavier than their internal combustion engine vehicle (ICE) counterparts. The chair of the National Transportation Safety Board noted “The Ford F-150 Lightning is between 2,000 and 3,000 pounds heavier than the non-electric version.” Furthermore, the National Bureau of Economic Research found that adding 1,000 extra pounds to a vehicle increases accident fatality risk by about 47%.
Consequently, automotive OEMs face severe constraints in trying to design BEVs with enhanced range, safety and electronic content. It is one of the most formidable R&D challenges the industry has ever faced.
Despite the immensity of the challenge, these concerns for OEMs, consumers and legislators can be mitigated if the conventional overweight power delivery network (PDN) in EVs is replaced by 48V zonal architecture in which a 48V bus replaces legacy 12V system. Deploying a zonal architecture supported by high-density power modules will reduce weight in three ways. This new architecture will enable the transition from thick wire harnesses to a much thinner one, reducing harness weight up to 85%. Additionally, low-voltage auxiliary batteries can be removed and virtualized with power modules, completely eliminating the battery’s weight. Lastly, the PDN upgrade using power modules optimizes the thermal management system, reducing its weight by up to 33%.
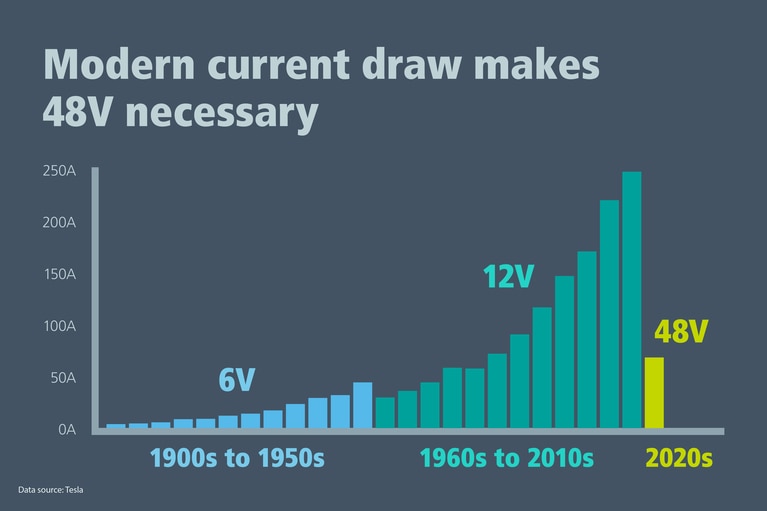
Figure 1: Conversion to 48V system reduces vehicle total current draw from over 250A to under 75A without impacting the electrical content of the vehicle. Since 1908, the current demand in automobiles has grown exponentially with the addition of vehicle electronics. In the 1960s OEMs increased voltage from 6V to 12V, causing current to drop for the first time in 60 years. Today, most OEMs still use the 12V bus, despite the demand for more current. In 2023 Tesla became the first OEM to announce a full transition to busing 48V throughout the vehicle, which will dramatically drop current demands.
So, transitioning to a zonal architecture, an alternative to traditional centralized architecture, significantly reduces weight and improves overall power system efficiency.
Moving to 48V: an obvious improvement and overdue for BEVs
New electronics like safety, security and autonomy have been added to new vehicles in every design cycle. Every additional feature increases the power draw and with a fixed, standardized battery, that has translated into an exponential increase in current. Evidenced by the trends in current (Figure 1), the centralized architecture PDN is unsustainable. The only way to support the ever-growing need for power while bringing back sustainable current levels and minimizing the wire harness weight is to increase the operating voltage to 48V using a zonal architecture.
Today’s BEVs are powered by a primary high-voltage battery (typically 400V or 800V) that needs to deliver power not only to the electric traction motor but also to a myriad of low voltage loads, like the air conditioner, heated seats and infotainment systems. A PDN steps-down the high voltage to the 48V and 12V auxiliary batteries that energize these subsystems.
Moving to a 48 zonal architecture presents an opportunity enabled by Ohms Law: Power=Current×Voltage. For the same power delivery, a 12V source requires four times as much current as a 48V source. Thus, the 12V wire also is generally four times thicker than a 48V wire.
The demise of the 12V centralized architecture
The 12V centralized system has been the traditional power architecture used in automobiles since the 1960s. This architecture consists of one bulky silver box housing which contains a set of discrete components, including all the DC-DC converters, high-voltage (HV) to 48V to 12V. Thick and heavy wires are required to carry the 12V current to the points-of-load. Moreover, due to legacy DC-DC conversion inefficiency, this centralized power system generates significant heat from the silver box, often requiring intensive liquid cooling, which adds more weight.
To transition to 48V high-density power modules can be used at the endpoints to efficiently convert to 12V at the points-of-load. This enables the OEM the flexibility to gradually transition the 12V load devices to 48V over time. This helps rapidly achieve the benefits of using 48V with minimal disruption to the system architecture.
48V zonal architecture reduces heat loss and current
This novel 48V zonal architecture system capitalizes on Ohm’s Law and is a paradigm shift for the industry, in which DC-DC conversion occurs closer to the points-of-load, rather than inside the centralized silver box. In this approach, HV-to-48V conversion enables safe 48V to be bussed throughout the vehicle. 48V-to-12V conversion occurs at the point-of-load. By carrying current at 48V instead of 12V, wires can be thinner, lighter and significantly cheaper (Figure 2). This smaller, more flexible wire is also easier to route within the vehicle. Additionally, this approach evenly distributes the heat losses associated with DC-DC converters throughout the vehicle, enabling the potential use of chassis-mounted heat conduction and convective air cooling.
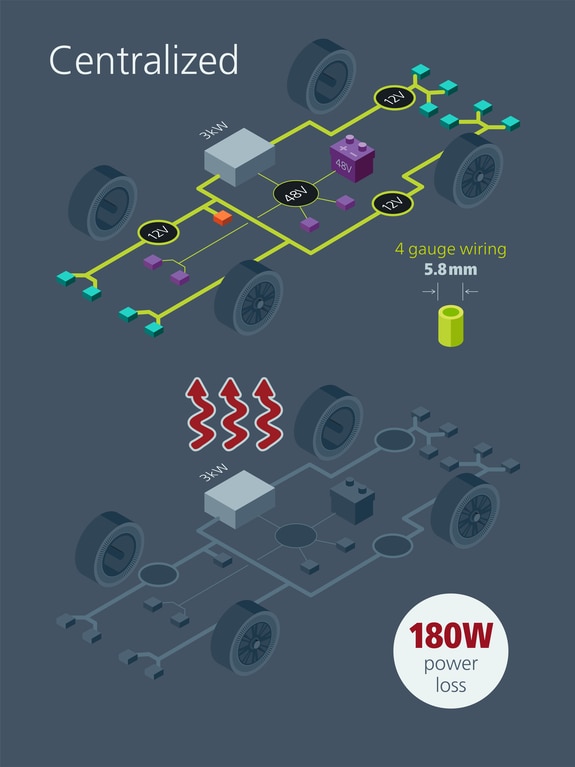
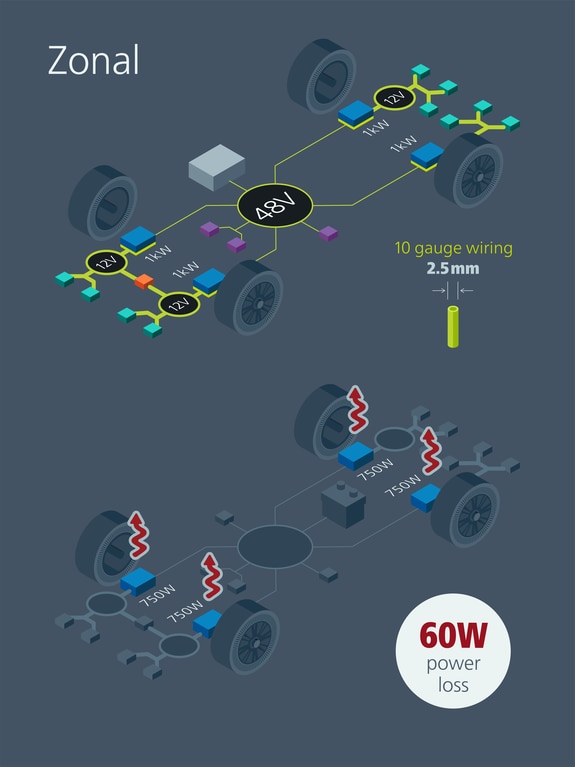
Figure 2a (left) & 2b (right): There are two distinct PDNs used in automobiles today. The 12V centralized architecture and fast-growing 48V zonal architecture. The former depends on the thick 12V wire harness, while the latter draws upon the thin 48V wire harness, which is far lighter, reduces heat loss and reduces current by a factor of four.
Counting up the weight savings
The 48V zonal architecture better supports the increasing power demand in BEVs, while simultaneously lowering vehicle weight in three ways.
- Wire harness: ~85% weight reduction
The upgrade to 48V zonal architecture means traditional 12V, 4-gauge wires at 273g/m, will be replaced with 48V, 10-gauge wires at 27g/m. This reduces the wire weight by approximately 85%. - Auxiliary battery elimination: ~100% weight reduction
A zonal architecture with power modules enables an acceleration of the DC-DC converter’s transient response, which creates a virtual battery. Therefore, zonal 12V/48V power modules replicate the characteristics of 12/48V low-voltage batteries, while completely eliminating the physical 12V battery, saving 100% of the weight. - Power system optimization: ~33% weight reduction
Substituting the zonal system for the centralized system moves the 48V-to-12V power conversion out of the silver box to the points-of-load. The revised power system box using high-density power modules to provide 48V output will be up to 33% smaller. Therefore, the housing weight can be reduced by up to one third (33%).
In the traditional 12V centralized system, discrete components create a high ambient temperature inside their silver box housing. The power system box using high-density power modules creates less heat, and the point-of-load modules can be efficiently air-cooled on the chassis. These improvements enable the liquid-cooling system to slim down by up to 7%.
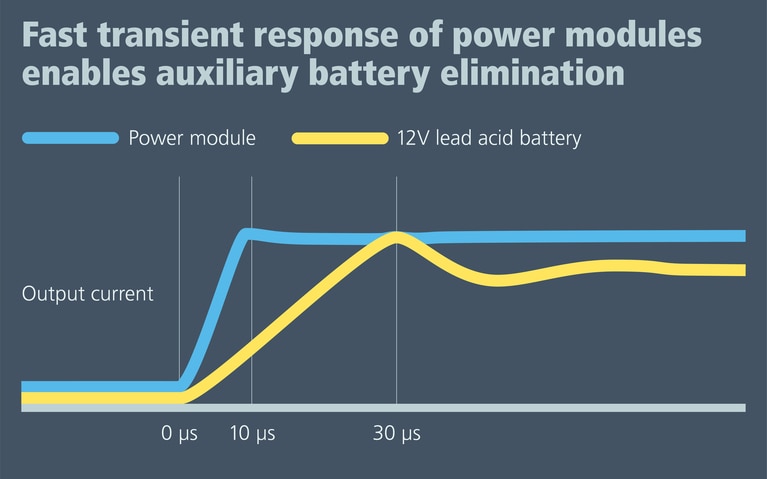
Figure 3: Power modules deliver a faster transient response than 12V lead acid batteries creating a virtual battery that can replace the legacy, heavy 12V battery.
Transforming weight into opportunity
OEMs accrue a variety of benefits by using a zonal architecture. To illustrate, consider the impact weight reduction will have on increasing range. Heavier vehicles tax power consumption and range.
However, extra weight can mitigate the impact on range if it is used to increase battery size. The additional battery provides more energy storage, improving range.

Bild 4: Das zentrale Gehäuse kann reduziert werden, wenn Leistungsmodule und eine zonale Architektur verwendet werden, da die Wärme an den Endpunkten, an denen 48V in 12V-Lasten umgewandelt wird, effizienter abgeführt werden kann.
In a study conducted by Vicor, zonal architecture supported by high-density power modules can reduce vehicle weight up to 40 pounds (Table 1). When this weight is replaced with 40 pounds of battery cells, the EV driving range can increase up to 4,000 miles per year, with no net weight gain. This is significant because the average American drives 14,263 miles per year, according to the Federal Highway Administration in 2023. Therefore, utilization of the 48V zonal architecture can reduce yearly recharging time by up to 30% (Table 2) and increase the distance the vehicle can travel on one charge.
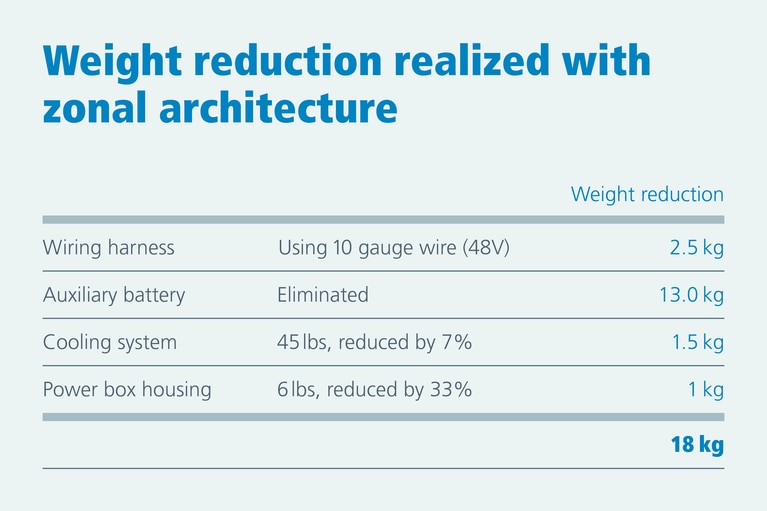
Table 1: A 48V zonal architecture used in conjunction with high-density power modules will save about 18kgs (40 pounds) in compact electric SUVs.
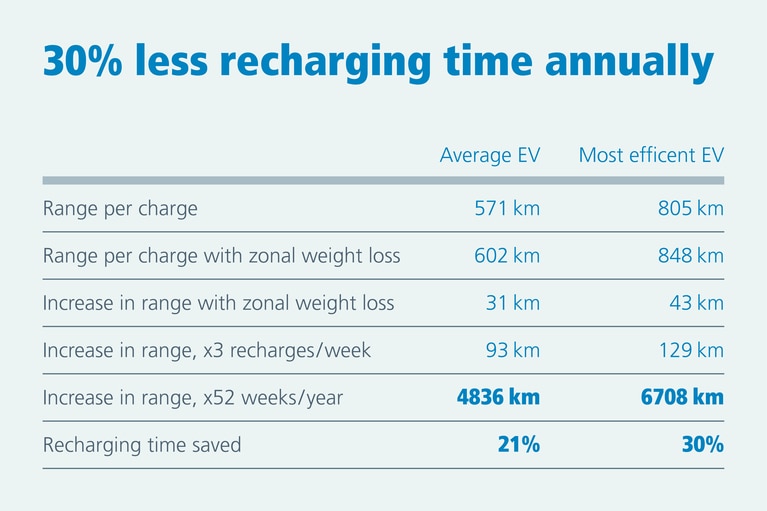
Table 2: Enhanced range offers drivers more distance per charge, reducing the charges needed per year.
Innovate to eliminate
Electric vehicles are overweight and this trend is neither sustainable nor beneficial to the overall growth of EVs. The 12V centralized architecture, with its legacy silver box and discrete components, needs to upgrade to 48V zonal architecture to optimize the EV power delivery network and thermal management system. Going zonal can increase range up to 4000mi/year or can be used for additional safety or electronic features. The most efficient zonal architectures use small, lightweight converters at the point-of-load. Highly efficient power-dense modules are the best choice for 48V-to-12V conversion. Given the complexity of the automotive power electronics today, OEMs need to be creative to save weight while increasing performance. Vicor, the leader in high-performance power modules, enables innovation and creativity. Vicor compact power modules, architectures and topologies offer automotive OEMs flexible, scalable power solutions for high-voltage power conversion throughout the vehicle. Easy-to-deploy power modules are the alternative to the traditional discrete designs used in a legacy centralized power system. Small, compact power modules also are the obvious choice and natural complement to a 48V zonal architecture, which is the future power delivery network for the automotive industry.
This article was originally published by Power Systems Design.
Related content

EV sales for both pure battery electric vehicles and plug-in hybrid electric vehicles are accelerating rapidly

High-density power conversion significantly reduces the size and weight of DC-DC conversion

On-Demand Webinar
YK Choi, Sr. Field Application Engineer at Vicor and YoungJae Kang, Chief Engineer at INFAC discuss how integrating 48V conversion into the battery pack will reduce heat, cost, and...
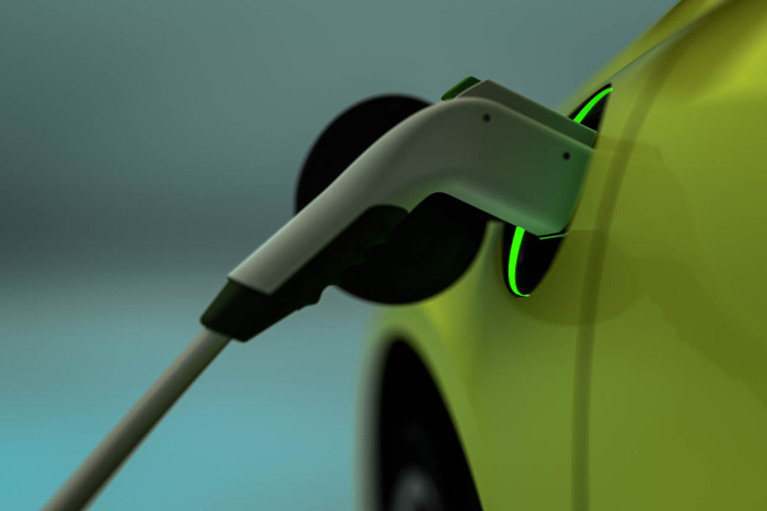
A vehicle has many different power requirements. A modular power approach is inherently more flexible and scalable, able to address these challenges