Article
Electric Vehicles: 48V is the new 12V
To meet the high performance demands of EVs, OEMs are converting from the primary battery (800 or 400V) to 48V to more efficiently distribute power to loads.
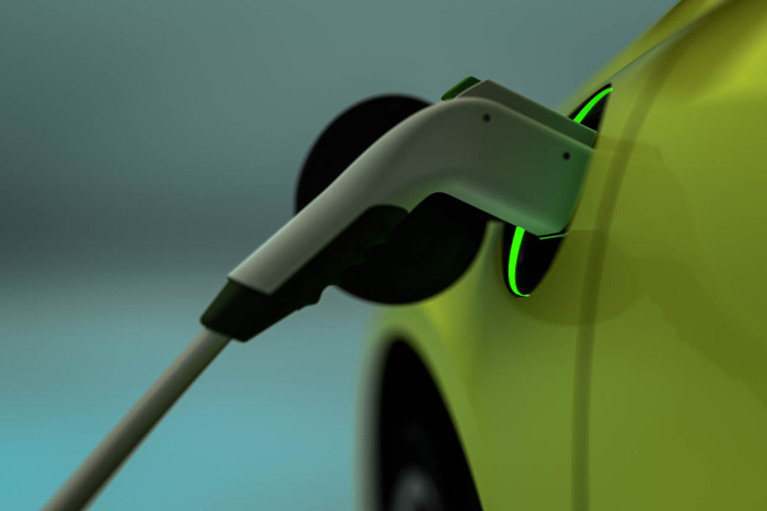
Electric vehicles (e-mobility) is perhaps one of the most significant challenges that technology companies and consumers have had to face in recent years. While there is an increasing need to find eco-friendly systems that can revolutionize the way we move, there is also a need to ensure that the new green technologies are as efficient and effective as possible in terms of price and performance.
Vehicle OEMs need to meet increasingly stringent CO2 emission standards while increasing vehicle performance to remain competitive. This significant challenge is addressed by electrification in pure-electric vehicles (EVs), hybrid-electric vehicles (HEVs), and internal combustion engine vehicles (ICEs). The addition of higher-voltage batteries such as 48V, 400V and 800V to meet the increased power requirements has, in turn, increased the complexity of power delivery architectures and posed new demands in terms of size and efficiency.
Mild-hybrid-electric vehicle (MHEV) systems are the gateway to electrification. Also identified as light-hybrid propulsion, they will contribute to the exponential growth of hybrid models. The MHEV system is capable of recovering vehicle energy during braking and provides energy during the restart of the vehicle, thus reducing gas consumption and CO2 emissions.
A second electrification approach for HEV models involves an electric motor working together with the ICE, enabling the vehicle to travel 100% in electric mode for a few kilometres. Another popular alternative is the plug-in hybrid-electric vehicle (PHEV), where the battery can be recharged by the grid, and the range at zero emissions increases to about 50 kilometres. In this case, the electrification is decidedly higher than MHEV and hybrid technologies—as are the purchase costs—with dozens of PHEV models coming onto the market.
Battery-electric vehicles (BEVs) lack an ICE and are instead powered by the combination of inverter plus electric motor. BEVs are rechargeable through the grid and during regeneration under braking. Among electric cars, we also find the extended-range electric vehicles (EREVs) with a small internal combustion engine used exclusively as a current generator to recharge the batteries when the level is low. The last category is represented by fuel-cell electric vehicles (FCEVs), which are powered by hydrogen‑fuel‑cells.

Figure 1: Global forecast by powertrain type (source: Vicor/HIS).
The solution could be not only in new energy storage technologies, such as solid-state batteries or hydrogen fuel cells, but also in improved car efficiency through weight reduction and new electrical architectures.
Today’s Electrification challenges
“Today’s challenges with electrification are the following: keeping costs down, meeting aggressive CO2 emission targets, managing change in power requirements, powering legacy 12V loads, delivering lighter, higher performing vehicles, increasing power levels, faster charging time and managing higher voltages from 800V and 400V battery systems,” said Patrick Wadden Global VP Automotive Business Development at Vicor Corporation.
Manufacturers of cars, trucks, buses and motorcycles are rapidly electrifying their vehicles to increase the fuel efficiency of internal combustion engines and reduce CO2 emissions. There are many electrification choices, but most manufacturers are opting for a 48-volt mild-hybrid system rather than a full-hybrid powertrain. In the mild-hybrid system, a 48V battery is added alongside the traditional 12V battery.
“There is either an 800- or 400-volt battery in the vehicle. Vicor takes either the 800 or 400 volts from the battery and converts the power to 48 volts for powering loads such as the electric turbo, headed windshield and cooling pumps. Systems that are powered from the 800- or 400-volt battery have the option of completely eliminating the 48V battery and creating a virtual 48V battery. This elimination of the 48V battery offers the OEM a higher power density, reduction of weight and size, all enabling an extended vehicle range. These solutions are scalable therefore addressing entry level to luxury vehicles,” said Wadden.

Figure 2: Conversion: enabling virtual 48V batteries.

Figure 3: Moving from an overloaded 12V mechanical to 48V.
48V technology efficiently distributes power
48V technology increases power capability by 4x (P = V • I), which can be used for heavier loads, such as the air conditioner and catalytic converter at start up. To increase vehicle performance, the 48V system can power a hybrid motor that is used for faster, smoother acceleration while saving fuel.
“Overcoming the hesitancy to modify the long-standing cost-optimized 12-volt power delivery network (PDN) may be the biggest challenge,” said Wadden. He continued, “for the automotive industry a 48V mild-hybrid system provides a way to rapidly introduce new vehicles with lower emissions, longer range and higher gas mileage and practical approach. It also delivers new and exciting design options for higher performance and features while still reducing CO2 emissions.”
The vast majority of centralized DC-DC converters used are bulky and heavy, since they use old PWM low-frequency switching topologies. A more up-to-date architecture to take into consideration is decentralized power delivery (Figure 4) using power modules.
“The benefits to using a decentralized model can be realized even more so at the system level with lighter-weight cabling around the vehicle: there are some nice benefits to placing the converter closest to the load in terms of minimizing impedance and resistance, some of the cooling methods can be simplified and in some cases one can eliminate a cold plate or liquid cooling. The option to implement functional safety with more options, and flexibility comes into play,” said Wadden.
This power delivery architecture uses smaller, lower-power 48V-to-12V converters. The decentralized power architecture offers significant thermal management benefits in a power supply system.
“Let’s look at a high-level diagram of a centralized system vs a decentralized system. On the left we have a traditional 3kW silver box, traditionally with a 400V input to an output of 12V powering 12V loads in the car. On the right is an example of how 48V is used around the car: the converter is placed right at the point-of-load, the decentralized model does away with the big silver box and spreads the power distribution as needed around the vehicle. This also allows for implementation of ASIL FUSA with redundant supplies. As the power requirements go up, it becomes more and more difficult to manage and to keep adding these older traditional silver boxes isn’t an option,” said Wadden.
New 48V PDNs must support legacy 12V loads with increased power requirements and new high-power drive, steering and braking systems using cables. Delivering more 48V power with an increasing number of loads requires high-density modules compared to larger, bulkier discrete solutions. Vicor offers several modules for power delivery from 48V. These devices include fixed-ratio and regulated conversion solutions that support both 48V and 12V loads in buck or boost mode. These converters can be contained in a single housing or distributed throughout the vehicle using a smaller and lighter 48V PDN.

Figure 4: Architecture: Centralized vs. Decentralized.
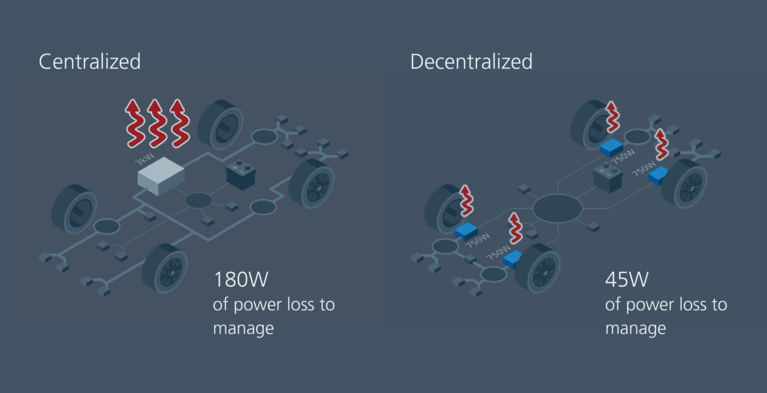
Figure 5: Managing power loss with a traditional converter at 94% efficiency.

Figure 6: Vicor solutions.
The Vicor NBM is used in a decentralized architecture whenever OEMs need to place voltage-conversion stages around the vehicle closest to the load and either stepping 48V down to 12V or boosting 12V to 48V.
With the use of 400V and 800V charging stations, the compatibility of the vehicle with any station requires a conversion solution that is as simple as possible but above all efficient. The NBM6123 provides 6.4kW fixed-ratio 400V and 800V conversion in a 61 x 23mm CM-ChiP package, enabling a scalable, high-efficiency, high-density solution for compatibility between roadside charging stations and different vehicles. The bidirectional capability of Vicor solutions allows the same module to be used for step-up or step-down conversion. The NBM6123 can also be used for power delivery to the vehicle for air conditioning during charging, minimizing the battery-balancing circuit.
Conclusion
The move toward vehicle electrification is taking many forms today and powering them is complicated. A vehicle has many different systems and each may have different power requirements. A modular power approach is inherently more flexible and scalable, able to address a myriad of these challenges. Vicor’s high-performance solutions are small and light-weight, designed to address power conversion, charging and delivery for any system.
This article was originally published by Power Electronics News.
Related content

EV sales for both pure battery electric vehicles and plug-in hybrid electric vehicles are accelerating rapidly

On-Demand Webinar
YK Choi, Sr. Field Application Engineer at Vicor and YoungJae Kang, Chief Engineer at INFAC discuss how integrating 48V conversion into the battery pack will reduce heat, cost, and...

High-density power conversion significantly reduces the size and weight of DC-DC conversion
Vicor power module transient response (75A/10µs), is three times faster than 12V, in essence creating a virtual battery